How to deploy the Model Based approach in an existing PLM
/in Uncategorized ArticleMews Partners has been built on the knowledge of our founders regarding the (Product Life-cycle Management) systems and how to successfully define the related processes, organisation, and supporting tools. In this article, we want to give back some of the knowledge and lessons that can be applied to successfully handle in the PLM, the brought by the introduction of new ways of working in managing Product and Manufacturing definition, focused on the usage of ‘models’ (Model-Based System Engineering, Model Based Engineering,…).
Historically, PLM systems have been built to answer to one very specific business need: How to maintain the coherence between the different teams and departments working on the multiple engineering disciplines (Product development, Production engineering, etc)?
30 years ago, this meant how does a business manage to maintain the consistency of evolutions of its definition dossier and manufacturing dossier, that was represented mostly by documents.
Since then, most of the industries have evolved to compile many other information than just documents, to describe and manufacture their products: schema (wiring diagram), 2D models (e.g. drawings), 3D models (Digital mock-up for Mechanical CAD is now widely used), data (simulation results, test results, torque value…). Ensuring all this data is organised, maintained coherently and available to anybody that needs it, is critical to successfully enable that the many teams (both internal but also external with customers and suppliers) can work concurrently on that data.
The volume and variety of information needed to be maintained has also increased over time, adding complexity for any company. This is a particularly challenging for multi-countries companies where the data shall be constantly exchanged between the different sites and services 24 hours a day.
Introduction of a new category of information in this landscape, the ‘Models’, is adding another complexity factor: how to correctly manage these models, their evolutions, their data inputs, their consistency with other models and product information? A stress simulation model would require information from the material of the part, from the 3D model, from the forces to be applied: each time, the correct ‘version’ of these information should be used with the correct ‘version’ of the simulation model.
Models are different than the non-structured information of documents because Models are structured information therefore it is easier to access its information, treat it or process it in comparation to a written documentation. Moreover, not like documents, Models allow us to manage the information continuity and consistency in a more automatized manner.
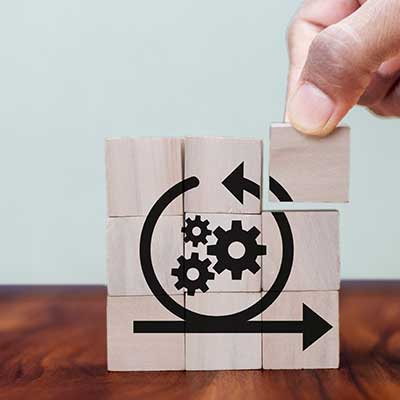
As increasingly more models are created by each function to serve their needs, how do we maintain coherence between them all and how do we extract the most value out of them? This can be achieved by making the PLM evolve to be able to manage these models, through what we call the ‘Model Based PLM’.
There are 3 lessons that must be considered to succeed in the transition towards a Model Based PLM:
1. Prepare enterprise functions and teams for changes caused by the Model Based approach
“All models are false, but some are useful”
The power of the models is that they aim to simplify reality and to provide a baseline of comprehension shared between people. Models can be quite simple, but they can be also extraordinarily complex, and its ease of use and manipulation can vary.
The implementation of Model Based throughout an enterprise is far from being a simple endeavour and many will resist to this change. To battle against that resistance, it is important to provide sense to the change. To do so, we recommend:
- Defining a minimum common data ontology to provide a strong basis of shared knowledge easing the deployment of both Models and PLM platform.
- Ensuring Model Based approach is already well understood and supported as it is a very important change in any organisation clarifying the main objectives and reasoning behind this deployment. A dedicated team in charge of training and deploying it and a clear governance must be set-up to provide perspective, progress in the overall project roadmap and to communicate frequently. These are the main key success factors of any successful transformation.
2. Synchronous approach (MB & PLM transformation)
Integrating the utilisation of Models in functions that usually do not use them is a big “step change”
If in addition, you add the layer of complexity of the implementation of a PLM platform to manage those new or old models you have a recipe for disaster. This is a well-known issue, experienced a few years ago by many companies when they introduced the 3D models for Mechanical CAD (MCAD): they had to find a way to articulate and synchronize the MCAD BOM managed in the MCAD tool (Catia, NX, Creo,…) with the full Product BOM manage in the PLM: this question of articulating the different product description information, is now reaching a new level of complexity with the use of Models in many other areas than just MCAD.
Historically many have experience with locally developed models that are not integrated in an overall dedicated PMT PLM as they are fit for purpose for the local requirements. That is one way of doing things, it eases model management (imagine a model stored only in one colleague’s computer), update and maintenance. In the other hand the company will not be able to leverage that local model with the added value of connecting it to the other functions: It is a trade-off, for sure, but we are convinced that the best approach if the model is so valuable is to manage it within the PMT framework and connectivity that a PLM can provide. Imagine having a 3D model of your plant: using it ‘standalone’ to optimize the position of the different machines in the shopfloor is already bringing value. But, connecting it with a logistic model describing the flow of the various parts, would bring another level of value to test different scenarios of machines positioning to optimize the flow of parts based on logistics inputs.
Our recommendation is to synchronize both changes (Model integration and PLM deployment) in one step to be organized as the same transformation. This combination has the following advantages:
- You can combine the up skilling of the usage (definition, design, and exploitation) of new models with how these models must be managed in coherence with the rest of the enterprise.
- You can much easily provide a context of these new models inside of the enterprise and through their usage a better comprehension of the links between models of other functions.
- It allows for a better mastering of the requirements to manage the new Process Methods and Tools of the PLM platform with practical usage.
3. Adapt Data management to Model Based approach throughout the system lifecycle
In a physical product development, production optimisation and proactive maintenance driven approaches, not all data is important
Trying to manage every single data, in every single dimension, would be an impossible task… for a minimum added value.
Our conviction is that it is key to find the minimum set of data relevant for each function in a business, provide context for it and link it to its interfaces in a way that makes sense. Therefore, being data driven means that the data that is important is taken care in a way that it provides the most value to the business. In the case of the increasing number of models created by the business that completes the overall definition dossier, sales dossier, maintenance dossier, etc, the key is to understand what data needs to be consistent with the other functions on how that data circulates through the company.
Once you understand that, you will be able to adapt your PLM in a way that makes the most sense to you and your company and therefore making people adhere to your vision easily. In another words, you will be able to translate the business requirements from the distinct functions to modify or improve your PLM to manage the optimal levels of granularity of the Models in configuration. As for documentation we used to manage the versioning of the whole documentation the question would be: for my enterprise what do I want to follow in configuration for the Models? The whole model? Only the information? A combination of both? What about of the parameters that the model receives as inputs or set-up?
In conclusion
With the increase of complexity, companies have no choice to combine Model Based approach with existing PLM platform deployment. Nevertheless, this brings challenges:
- What is the right level of information to connect between the different Models, and the different Data?
- How to bring the most value of this interconnection, without drowning in the details?
- How to embark all the teams in this new journey that will change their way of working (defining models) and way to exchange with other teams?
These challenges must be faced head-on:
- Preparing it: defining the vision and the sense for the company (Change Management) and defining a common language between all functions (Ontology definition).
- Communicating clearly: By understanding and answering to the needs of the end users and providing accurate information on the progress made and difficulties encountered that may impact company operations that need a dedicated escalation or decision from management.
- Focusing on the data that is useful: by finding the sense of what is important to the business to what is not (Data driven approach).