We had the chance to chat with Robert Heidsieck, Director of Circular Economy at GE HealthCare. Together, we shared the new challenges and opportunities aligned with developing best practices within the healthcare sector. Let’s get into it!
1. What is GE HealthCare’s position on the circular economy?
The concept of the circular economy is not new to GE HealthCare. In fact, medical equipment is a critical asset, designed to be reliable and maintained for long term use. The company promotes practices aimed at improving product durability, maintainability, and life extension, in a circular model of updating, reusing, repairing, refurbishing and recycling.
To this end, GE HealthCare has developed an efficient supply chain, using remote diagnostic capabilities, intelligent maintenance systems, and product extension programs. It also ensures the traceability of its equipment, making it possible to buy back systems at the end of their life cycle, in order to upgrade them for new customers or to recover parts for equipment maintenance. The circular economy is part of the company’s DNA.
Here are a few examples that illustrate the importance of these elements in the development of our product ranges. With regard to sustainability, we note that a quarter of our imaging systems have been installed for over 15 years. Around 100,000 of these systems are maintained using repaired or reused parts every year. Manufacturing X-ray tubes uses over 100 tons of recycled material in a closed circular loop.
In 2023 alone, we completed 338 MRI upgrades as part of a program to extend the lifespan of our machinery—a program that has since seen rapid growth. We buy back ~7000 systems and recycle 4,450 tons of material per year.
All these initiatives are good for the environment. However, if we are to guarantee access to healthcare for all, while reducing our environmental impact, we need to go much further. This is becoming both a regulatory requirement and a growing expectation on the part of our clients.
The turning point came 3 years ago when a number of our European clients included environmental criteria in their proposal requests.
We were then facing 2 main challenges:
- The first was to measure our environmental impact and identify relevant levers. We had to change our habits and initiate a process to collect the information associated with our environmental aspects;
- The second was to communicate this information to the rest of the company, and to support change while instituting new practices in order to erase preconceptions and preconceived ideas.
To meet these challenges, GE HealthCare developed a number of company-wide initiatives. One of these initiatives is the creation of a department dedicated to tracking the eco-circularity of products throughout their life cycle, of which I am the director.
Throughout my career at GE HealthCare, I’ve been lucky enough to contribute to various aspects of the circular economy— from research and design, overseeing the equipment supply chain, and after-sales service, to operational activities in product lifecycle management (focusing on repair, reuse, refurbishment, and product life extension programs). This well-rounded experience is an asset for my role.

Source: GE HealthCare LifeCycle Solutions Circular Economy
2. In concrete terms, what is the role of your team?
The complexity of our product lines and supply chains, as well as the wealth of deposits linked to the size of our installed range of products, are such that it’s difficult to ensure optimal use of eco-circularity opportunities.
Our role is to show how the circular economy can accelerate both the decarbonization of the healthcare industry and our products through innovation, collaboration, and concrete case studies with business experts. We can be seen as a center of experimentation and innovation within the company, a laboratory for accelerating circularity opportunities for our products through concrete use cases… We learn by doing. We provide expertise and methodologies to operational teams, who are themselves experts in their own fields. We help them adjust their practices, through data analysis (Life Cycle Analysis–LCA, failure analysis, etc.) in concrete and often critical situations. The aim is to identify together which components can be reused, repaired, or maintained, and which materials can be sourced via recycling channels.
Maximizing re-use and minimizing waste are vast subjects, and there are huge opportunities in both areas. Take Magnetic Resonance Imaging (MRI), for example. The most powerful MRI magnets can weigh up to 8 tons, which means they have to be transported and built on site. To bring a clinical site to the cutting edge of diagnostic, application, and environmental performance, we have an upgrade program that keeps the magnet on site and only modifies the surrounding structure. This significantly reduces the environmental footprint by bringing the latest in clinical functionality through new electronics and technologies. We carry out these operations directly on site to avoid logistical constraints and cut costs. It’s an extremely innovative model. We are looking to maximize opportunities for circularity with replaced parts and extend this model to other products.
3. Does the company’s management have any specific ambitions for the circular economy?
Absolutely. In 2023, Peter Arduini, CEO of GE HealthCare, committed the company to ambitious greenhouse gas (GHG) reduction targets as part of a Science Based Targets Initiative (SBTi) program.
SBTi is designed to help companies set science-based targets for reducing GHG emissions. Joining an SBTi program means that the company commits to significantly and measurably reducing its GHG emissions, using methods validated by SBTi.
GE HealthCare is committed to :
- a 42% reduction in operational GHGs by 2030
- a 25% reduction in GHGs from scope 3 products – supply chain – by 2030
- carbon neutrality by 2050
At the heart of the environmental section of our Corporate Social Responsibility (CSR) report are the two main sectors of eco-design and the circular economy. The circular economy is therefore considered a key element of our environmental policy.
However, we have to transfer these strategic goals into what our team implements on a day-to-day basis. Driven by customer expectations and the arrival of new regulations such as the Corporate Sustainability Reporting Directive (CSRD), we are working daily to innovate our daily practices.
4. What portion of sales is reflected within your circular economy model?

The rules for deeming income to be part of the circular economy are extremely complex, particularly in the context of the European taxonomy. For example, when selling refurbished spare parts or a second-hand system, even the packaging must comply with circular constraints: it must be made from at least 65% recycled materials, or come from a circular economy loop.
In reality, the rules are so strict that practices that would seem natural in the context of the circular economy (maintenance, product life extension, second-hand, equipment upgrades, etc.), don’t fully meet the established criteria. That’s why I can’t give you an official sales figure. However, I can assure you that these revenues are not marginal in the company’s overall income.
5. What are the main targets for your products within the circular economy?
Our strategy is based on various targets:
- Maximizing the opportunities offered by the circular economy: product simplification, repairability, product life extension, product upgrading, refurbishment and resale, re-use of parts, valorization of recycling actions.
- Re-designing components with high environmental impact. Over the past two years, we have heavily invested in integrating life cycle assessments (LCAs) into our projects. We have several case studies underway which have helped us improve both our operational processes and our products. That said, we still have work to do to systematize these practices throughout the company’s decision-making processes. In particular, it’s imperative to carry out assessments of the environmental impact of products, notably through LCAs, in line with European definitions of critical materials.
- Extending product lifespans. We have several programs dedicated to extending product lifespans. For example, we reuse spare parts from equipment in its declining phase to ensure the maintenance of sites remaining on the market. We also have a research program to extend the life of a repaired spare part through opportunistic maintenance techniques. In addition, we monitor our own indicators to assess spare parts consumption by system, in order to identify potential discrepancies. This involves a strong commitment from our engineers to collecting and analyzing maintenance data, and creating accurate diagnostics.
- Simplify and optimize reusing packaging. We are working to reduce the percentage of waste generated when our systems are delivered. Far too much packaging is thrown away after a single use.
- Extend our ecosystem to the hospital sector. We currently have two projects in collaboration with French hospitals to understand and improve the environmental impact of clinical procedures carried out as part of a healthcare pathway. In these studies, we are looking at the impact of the entire clinical ecosystem for carrying out medical procedures, which by its very nature goes beyond the impact of our equipment alone.
6. How important is data management in implementing these circular strategies?
Data is key to implementing decision-support strategies that optimize economic and environmental impact while preserving resources.
We have a vast amount of data available from a variety of sources. Unfortunately, this data is not always exhaustive or sufficiently accurate. We work with cross-functional teams (R&D, Production, and Service) to determine the best estimates in cases where direct data is incomplete. We are currently investing in data science to help us identify critical data and refine our estimates.
We are also working with our suppliers to ensure consistency in the flow of information about the environmental impact of the materials we source.
Ultimately, we envisage creating digital twins (dynamic virtual replicas) of all or part of the company. This would be a major step forward in controlling information flows and understanding their long term environmental impact. A great deal of information is already available, and we are actively working on this subject.

7. What were the main difficulties you encountered and how did you overcome them?
We have several teams dedicated to environmental aspects: eco-design, responsible purchasing, packaging improvement, and CSR teams. This organization enables us to concentrate our efforts and achieve concrete results. However, a great deal of coordination is required to ensure consistency. Ultimately, the aim is to define principles, standards, and metrics so that each team can integrate sustainability principles consistently into their actions. Circularity would then be a foundational component of current practices, sidestepping the fragmentation of team efforts and ultimately reinforcing our overall impact.
On the other hand, many similar initiatives already exist within the company, and we are working to implement strategic thinking with ramifications across all corporate functions. We are fortunate to be part of this paradigm shift and to influence it.
8. We understand that there are many challenges to making business models more “circular.” How can we continue this in-depth transformation?
Thanks to numerous internal resources, we are making better use of our waste. However, we need to go even further and recover it more effectively, because the external environmental impacts often underestimated. While we have made progress in managing the flow of incoming materials, we need to rethink the notion of the company as an extended enterprise. Conceptualizing the flow of outgoing materials remains under-exploited.
We therefore need to rethink our approach, not only to design systems for a circular strategy, but also to question the complete lifecycle of our materials. Although we are capable of designing recyclable products, there is still a real gap between theory and practice. The question remains: what actually happens to the materials generated by our activity? To move forward, we need to build meaningful collaborations and work towards more effective integration of circularity into our processes.
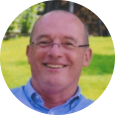
Robert HEIDSIECK
Director of Circular Economy at GE HealthCare